
What are Estolides?
December 18, 2019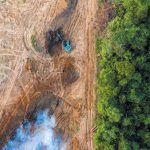
A New Way Forward
March 1, 2020Health and safety are priorities for food, drink and drug manufacturers.
Standards of cleanliness and hygiene are as important on the shop room floor as in hospital operating rooms. But when it comes to production equipment, lubrication keeps the business of feeding and healing the nation on track.
Lubricant leakages and maintenance are an inevitable part of all industries.
Lubricants do not discriminate against the materials with which they come into contact. So the food-processing and pharmaceutical industries have additional challenges in selecting the right lubricants to do the job. This article looks at the previous, current and future standards relating to lubrication in this industry.
Food-grade lubricants must perform the same technical functions as any other lubricant.
They provide protection against wear, friction, corrosion and oxidation, dissipate heat and transfer power, be compatible with rubber and other sealing materials, as well as provide a sealing effect in some cases. In addition, different applications within the food and drugs business demand that lubricants resist degradation from food products, chemicals and water/steam, must exhibit a neutral behavior toward plastics and elastomers, and have the ability to dissolve sugars. These oils must also comply with food/health and safety regulations, as well as be physiologically inert, tasteless, odorless and internationally approved.
The United States Department of Agriculture (USDA) created the original food-grade designations H1, H2 and H3. The approval of a new lubricant and its registration in one of these categories depends on the list of the ingredients.
- H1 lubricants are food-grade lubricants used in food-processing environments where there is the possibility of incidental food contact.
- H2 lubricants are food-grade lubricants used on equipment and machine parts in locations where there is no possibility of contact.
- H3 lubricants are food-grade lubricants, typically edible oils, used to prevent rust on hooks, trolleys and similar equipment.
Deciding whether there is a possibility of contact is tough, and many have erred on the side of safety with respect to selecting H1 over H2.
Currently, each component in the formulation is submitted to NSF by the lubricant manufacturer along with other supporting documentation. This is then reviewed to verify it is within the FDA list of permitted substances.
NSF is not the only organization working this area.
A joint effort by three recognized industry professional associations – the National Lubricating Grease Institute (NLGI), the European Lubricating Grease Institute (ELGI) and the European Hygienic Equipment Design Group (EHEDG) – developed a Joint Food-Grade Lubricants Working Group. This group has been active in drafting an authorization program for food-grade lubricants and developed DIN V 0010517, 2000-08 (Food-Grade Lubricants – Definitions and Requirements). There have been plans to use the DIN standard to develop an ISO (International Standards Organization) standard.
Understanding the differences between H1, H2 and H3 lubricants and making the proper lubricant selection is critical to food safety and machine reliability.
Biosynthetic Technologies’ Estolides are natural, sustainable, biodegradable and non-toxic. We believe lubricants should increase the efficiency and profitability of your operation while being safe for consumers and the environment. Our food grade lubricants are NSF H-1 registered and meet the requirements for a USDA H-1 quality lubricant and the requirements of the United States Code of Federal Regulations 21CFR 178.3570, 178.3620(b), and 573.680 of the United States Food and Drug Administration’s Regulations. Using acceptable USDA and FDA preservatives, our H-1 lubricants effectively control, inhibit and slow the growth of bacteria, yeast and molds that may occur from incidental contact. Our rust inhibiting additives give our food grade lubricants the strength they need to shield surfaces against rust and corrosion for extended equipment life. Rust-free surfaces also make it easier to keep equipment clean for safe food and pharmaceutical processing. When formulated with advanced anti-wear and extreme pressure additives, our H-1 Estolides significantly reduce friction and wear. Mechanical components can move smoothly and efficiently without causing metal-to-metal contact. BT Estolides come with a variety of superior benefits, meet international standards, prevent bacterial growth, reduce corrosion-related failures, protect components from wear and consistently produce results you can rely on!
That’s why we designed our Estolides to be a key ingredient to any final food grade lubricant application. This ensures to not only allow them to last longer in harsh environments but to also keep equipment running in peak condition.